How Collaborative Robotics Can Increase Your Business Productivity
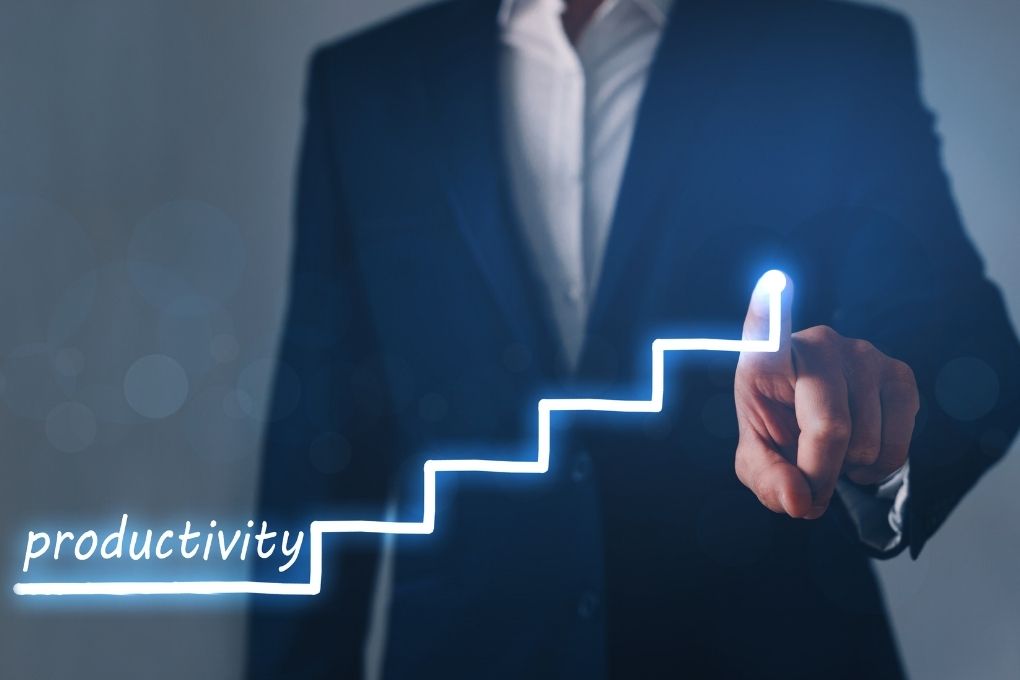
We live in an extraordinary era, dominated by technological revolutions, which began with the first industrial revolution and resulted in the incredible technological innovation of recent years. The emblem of these technological innovations can be found in the world of factories.
In fact, in recent decades, factory work has changed radically, leaving more and more space for automation. If once the figure of the worker could be considered unskilled labor, today this figure, more than a simple performer of repetitive tasks, is a highly qualified professional in the use of complex machinery.
The Robotic Arms
An example that best represents the processes described above is the robotic arm, also called collaborative robot.
Introduced over the past decade by companies such as Universal Robots, robotic arms have fundamentally changed the architecture and arrangement of people and machines within the factories that have adopted them.
Thanks to these devices, in fact, the segregation of spaces, that is the separation between machines and humans, typical of modern factories, is lacking. When this innovation is introduced, there is a mixture of the different workplaces and a sharing of spaces and areas between men and machines.
Automation through robotic arms guarantees an increase in production performance. Operations such as screwing, assembly, gluing and painting greatly increase their productivity.
The great advantage deriving from the use of these machines is not only linked to the increase in productivity, but also to the saving of space.
Collaborative robots, in fact, have such a small footprint that they can be integrated into any production plant, without necessarily having to change the architecture of the plant.
The Boog Case
Once we have listed the great advantages of using mechanical arms, we just have to offer you a practical example. We want to talk to you about the BOOG Machining Company case.
The company in question specializes in the production of small components machined with a lathe and milling machine.
The company turned to Universal Robots to increase the productivity of its plants, using machinery that could automate production and that could be easily and quickly programmed by its employees.
The second objective, but not least, was to prevent and reduce the health problems of workers related to manual production.
To achieve its objectives, Boog has selected a collaborative robot UR5, which is characterized precisely by its ability to handle small components, therefore perfect for the purpose.
Thanks to the implementation of the UR5 collaborative robot, to date, Boog uses only one employee, who loads and unloads the machine every three hours. Before this innovation, the same employee was forced to constantly monitor the machinery.
The introduction of the boom has resulted in increased productivity, freed up valuable resources for the company, and dramatically reduced employee occupational injuries by reducing the number of hours in contact with workers’ sharp components.
Finally, as regards the training of the workers, it was not complicated to instruct the workers in the use of the robotic arm. In fact, in just half a day of training, all workers were able to use the software of the UR5 robot.
Also Read: Digital Transformation, An Ally Of Sustainability